A look into the future of EV batteries
Wednesday 26th February 2025
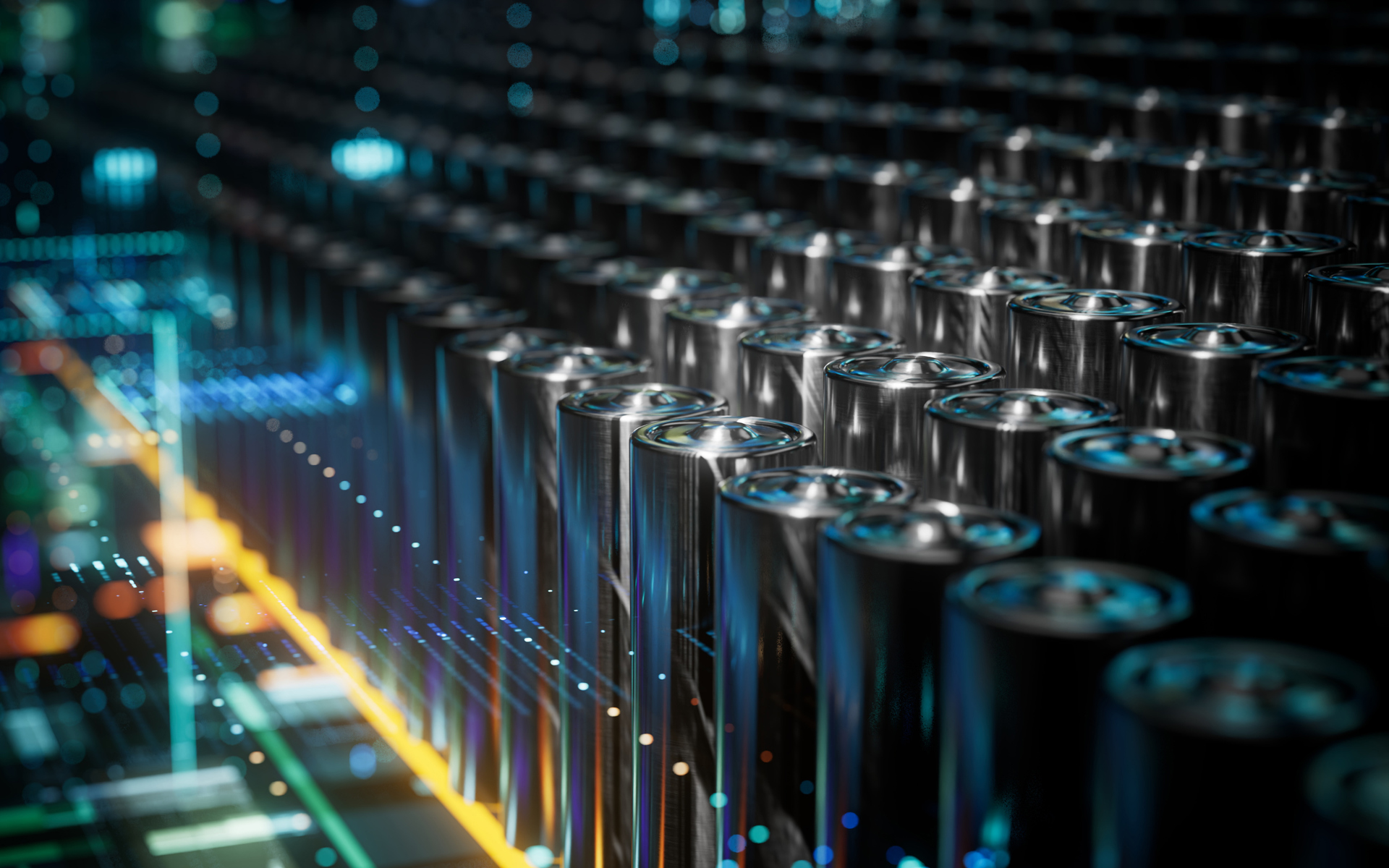
There’s no doubt that EV batteries have come a long way in the last few years and, thanks to significant improvements in real-world range, reliability, and efficiency, more people than ever before are getting into an electric car for the first time.
A battery is generally the single most expensive component of an EV and so, in many ways, the future of electric vehicles is inextricably linked to their primary source of power. So, what does the future hold for EV batteries?
Competing technologies
We often think about EV batteries as just one thing, whereas, in reality, there are a number of different technologies currently under development.
As the President of Toyota’s BEV factory in Japan, Takero Kato, said in a 2023 speech, “we will need various options for batteries, just like we have different variations of engines, because it is important to offer battery solutions that are compatible with a variety of models and customer needs”.
Currently, almost all EVs use a lithium-ion (Li-ion) battery that’s not much more than a scaled-up version of the battery in an average smartphone; the biggest difference being that an EV battery uses thousands of Li-ion cells in a pack. It’s a technology that works well, and has helped manufacturers produce some very impressive vehicles, but are we rapidly heading towards the technology’s optimum point in terms of range, weight, and lifespan. Not to mention the environmental concerns relating to the mining of raw materials.
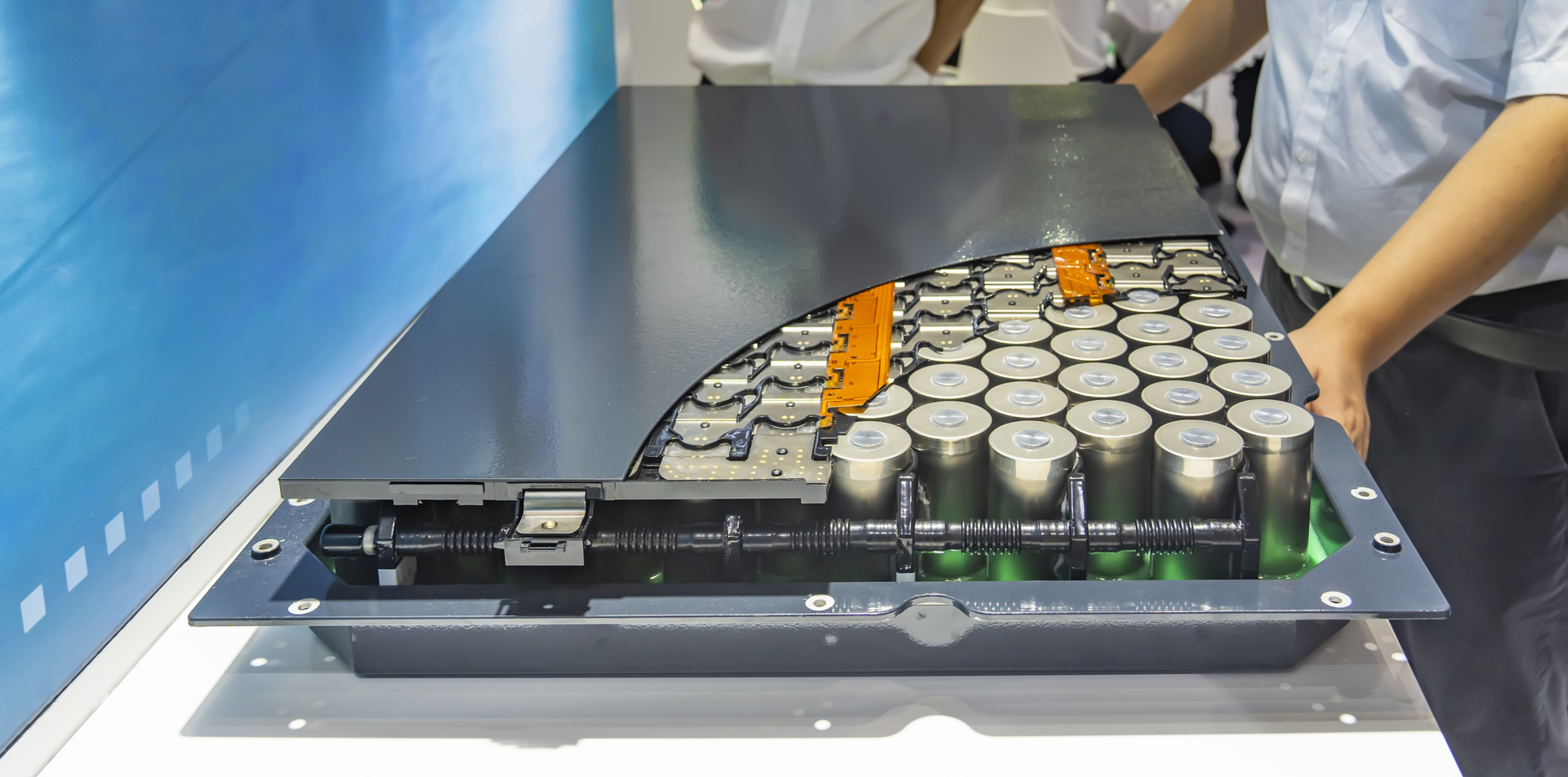
Solid-state batteries (SSB)
A solid-state battery works much like a traditional lithium-ion battery; however, instead of a liquid electrolyte sitting between the cathode and the anode, there’s a solid block made up of ceramics, polymers, or even glass.
Solid electrolytes have the potential to achieve a much higher energy density, which in turn means a longer range. They are also quicker to charge, slower to degrade, and there’s far less risk of ignition. Additionally, removing both the liquid and the separator allows solid-state batteries to be thinner, lighter, and more compact.
Depending on the chemistries involved, solid-state batteries use more lithium and are arguably more difficult to recycle. That said, they often use far less cobalt and nickel. There are also new methods of mining lithium being explored, including the use of geothermal wells. Put all this together and the overall reduction in climate impact could be as much as 39%.
Scaling up the production of any new technology is never easy, and this tends to make things more expensive in the short term, but SSB specialists Factorial have already formed partnerships with Mercedes-Benz, Stellantis, and Hyundai to create a commercially viable mass-market product.
Factorial’s Solstice™ battery uses a sulphide-based solid-state electrolyte material, which Mercedes hopes will enable them to build new EVs with up to 80% more range by the end of the decade.
Semi-solid batteries
While we await the widespread availability of solid-state technology, several manufacturers are developing semi-solid (or quasi-solid) batteries, which use a more viscous gel instead of the liquid electrolyte found in most EVs.
Using a polymer-infused gel allows for the replacement of graphite anodes with higher energy density lithium ones and the increased stability also reduces the need for cooling systems and other structural components.
To understand what this means in practice, the L6 saloon, currently sold by Chinese manufacturer IM Motors, uses a semi-solid battery that has 33 kWh more battery capacity without increasing the size. The result is a 28% improvement in range, taking it from 485 miles on a single charge up to 621 miles. It’s a similar story with one of their major competitors, NIO, who claim that the 150kWh semi-solid-state battery pack in their ET7 can deliver around 620 miles on a single charge.
Closer to home, Stellantis has announced that they will launch a demonstration fleet of all-new Dodge Charger Daytona vehicles that are equipped with Factorial’s FEST® battery technology. They say that this demonstration fleet will ‘enable the validation of Factorial’s technology and provide an assessment of its performance in real-world driving conditions.’
In many of the press releases, they refer to the FEST battery as solid-state but, if we look a little closer, we see that these actually use semi-solid electrolytes, with a lithium-metal anode, and a high-capacity cathode.
While this might seem no more than a halfway house, Factorial currently sees semi- or quasi-solid batteries as an important development that combines the performance and safety of solid-state electrolytes with the manufacturability of lithium-ion batteries.
Next-gen liquid electrolytes
With all of the attention on semi- and all-solid-state batteries, you would be forgiven for thinking that liquid electrolytes will soon be a thing of the past. However, Toyota disagrees and their battery technology roadmap includes maximising the potential of liquid electrolytes, with a promise of 600+ mile range by 2026. That said, some of those extra miles will come from improved aerodynamics and reduced vehicle weight.
Toyota also plans to expand the use of bipolar batteries, initially developed for hybrid EVs, to its battery-only models, thus increasing range and lowering production costs.
The term bipolar comes from the fact that, rather than each cell having its own set of positive and negative terminals as current collectors, each terminal is shared between adjacent cells, with the positive side of one cell and the negative side of the next applied to opposite sides of the same terminal. These bipolar electrodes are then stacked together, creating a series of connections within the battery itself. This approach has a number of advantages, as sharing current collectors between cells allows for a more compact and lighter battery design and the larger current flows offer a higher power output.
Looking slightly further ahead (2027/28) we could see a high-performance lithium-ion battery that combines a bipolar structure with lithium-ion chemistry and a high-nickel cathode to give a 20% boost in range.
Toyota is not the only company pushing the boundaries, with a number of EV battery manufacturers increasing energy density by simplifying battery structures so that, rather than packing lots of cells into smaller modules, and then lots of modules into a big battery pack, modules are being removed in favour of a direct cell-to-pack approach. On the plus side, this reduces packaging overhead and helps to improve energy density at the pack level, but it can also make repairs more complex to carry out.
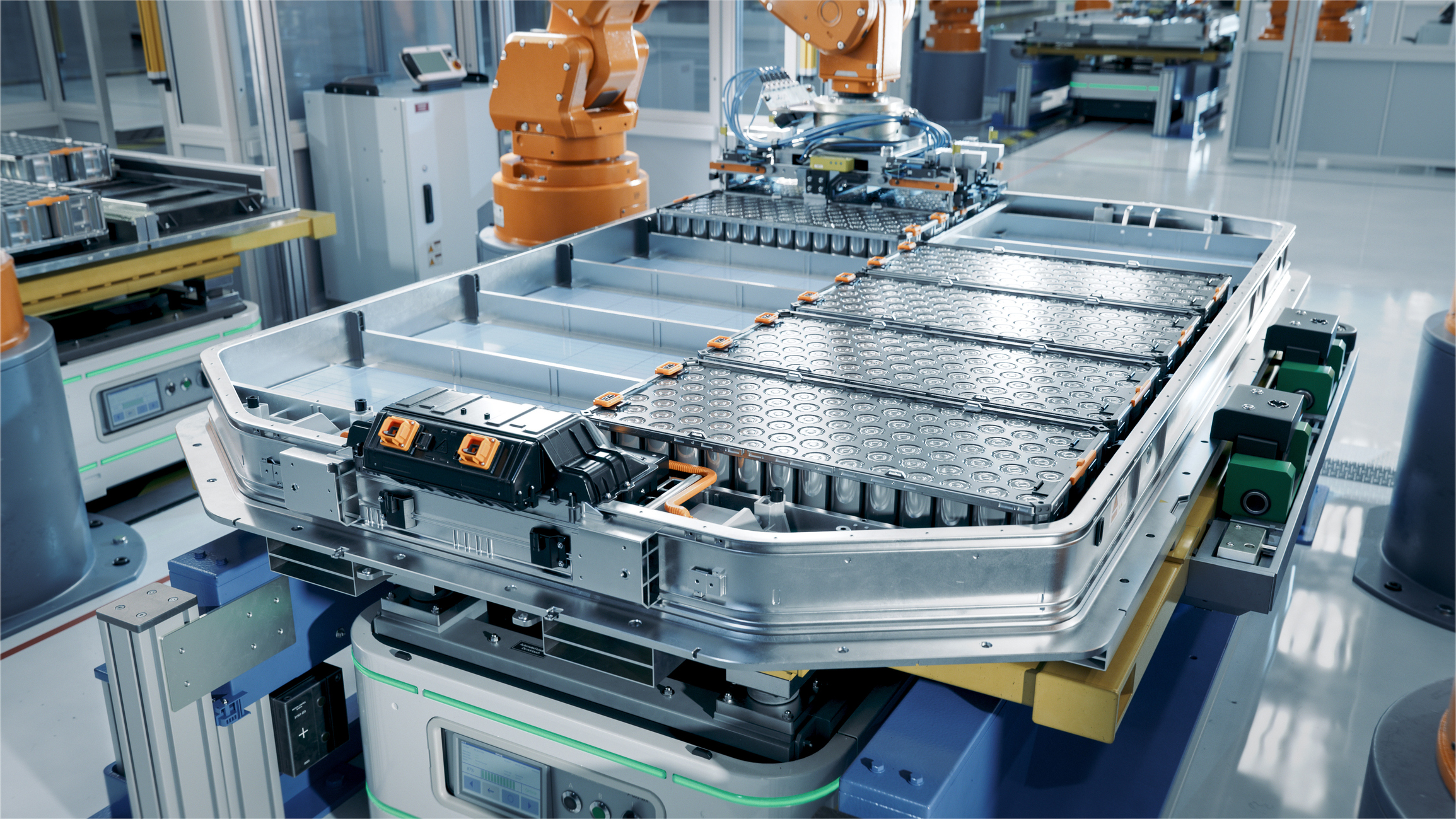
Lithium-sulphur batteries
As the name suggests, lithium-sulphur (Li-S) batteries use a sulphur cathode. In theory, this offers a number of advantages in that sulphur is both abundantly available and can be produced at a lower cost than existing compound materials used in lithium-ion batteries. Li-S batteries don’t use nickel, cobalt, or manganese, resulting in a c.60% reduction in carbon footprint.
It’s still early days, but Stellantis is investing in the development of a technology they claim has the potential to deliver more than twice the energy density of lithium-ion batteries and offers an alternative, non-nickel-manganese-cobalt cathode solution. Unfortunately, there are still quite a few challenges to overcome, including significant issues with battery lifespan and corrosion.
Sodium-ion batteries
Sodium-ion batteries (SIB) have a number of advantages. They don’t contain lithium or cobalt, sodium is plentiful worldwide, and the overall cost of battery production is thought to be 30% cheaper than lithium ion.
The downside is that an SIB has a low energy density, and this means heavier batteries and a shorter range. They do however work better than Li-ion in freezing temperatures. Overall, this means that sodium-ion batteries are best suited for short-range or specialist applications.
Innovation easier than commercialisation
There are many more battery innovations which may, or may not, bear fruit at some point in the future. This includes cobalt-free lithium-ion batteries and graphene batteries, which work in a similar way to lithium-ion batteries but with graphene-enhanced components that improve charging speeds, energy density, and lifespan.
The challenge is that even with a great innovation it takes around 10 years from startup R&D to first production and substantially longer to achieve a commercially viable offering, during which time existing technologies continue to improve, making the incremental benefit of alternative solutions far less attractive.
For example, the development of batteries that also serve as structural components of a vehicle has the potential to reduce weight, improve safety, and simplify production. The problem that remains is that, although the driving range is thought to be around 70% more than current battery technology, the adoption of semi and all-solid-state batteries could make this an insufficient gain to warrant the long-term research and development required for a mass-market rollout.
No single solution
As we’ve seen, there is a variety of different technologies being developed, all of which have pros and cons in terms of range capabilities, cost of production, and sustainability. As a result, rather than a single solution, there is likely to be a range of options to choose from based on what is most important to your business and drivers.
The good news is that whatever the future holds for EV batteries, we’ll continue to help you understand the available options and what they mean economically, operationally, and environmentally. To find out more about how we can help, just get in touch.